* 자재소요계획 (MRP: Material Requirement Planning)
제품의 생산에 소요되는 자재의 수량과 준비 시점을 결정하는 방법론 혹은 수량과 시점에 대한 계획
자재소요계획에서의 자재는 생산에 소요되는 부품, 원료 등 광범위한 원자재, 부자재를 의미.
좁은 의미의 자재: 소재, 원료
* 생산운영 계획의 일반적 단계와 구조 (이전 생산운영계획의 종류와 구조 글 참고)
전략적 생산용량계획(장기, 추상적, 총괄적, 전략적) -> 판매 및 생산 계획,총괄 계획 (중기) -> 주 일정 계획 (중기) -> 자재소요계획 (중기) -> (단기)일정계획 (구체적,상세,전술적)
* 자재소요계획의 목표 결과물
생산에 필요한 각 자재별, 가공, 구매, 조립의 시기와 수량에 대한 계획
* 자재소요계획 생성에 사용되는 정보
• 주일정계획: 개별 제품 모델별 생산 일정
• 자재명세서: 자재별 수량과 생산단계에 따른 상대적인 사전 준비 시기
• 자재별 리드타임: 사전 발주 시기 혹은 생산 준비 기간
• 재고 정보: 순 소요량 계산을 위한 재고 수준
* 주일정계획 (Master Production Schedule, MPS)
주일정계획은 제품 모델별로 AP보다 더 세분된 시기별 생산량 표현.
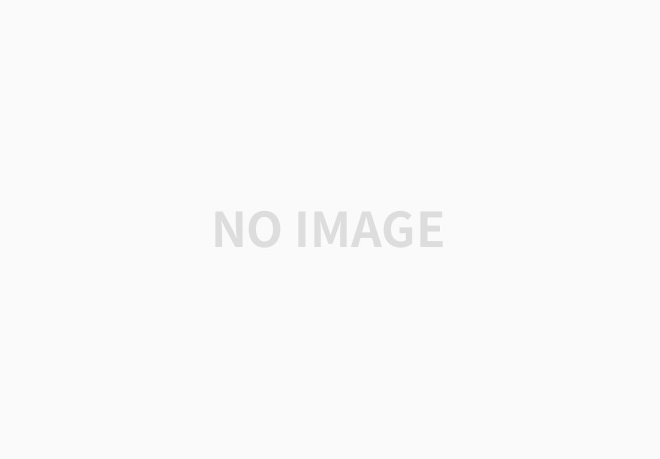
* 주일정계획 특징과 조건
• 총괄생산계획에 기반하나, 제품 모델별 생산량 계획, AP보다 세분된 시기별 계획
• 수요 예측과 선주문에 기반하나, 예측값이 아닌 계획값
• 제품별 납기와 연계될 수 있음
• 주일정계획과 수요를 참조하여, 예상 재고량 도출 가능
• 생산의 안정성을 위하여 계획변경 가능시한이 적용되기도 함
* 생산 유형별 상이한 MPS
• 계획생산방식의 완제품 기반
• 주문조립방식의 모듈 기반
• 주문생산방식의 고객 주문 기반
* 자재명세서 Bill of Materials (BOM)
자재들의 조합으로서 제품의 구성을 표현
• 부품과 중간재(sub‐assembly, 반제품)들의 연결과 계층적 종속 구조 표현
• 제품을 구성하는 부품의 목록
• 부품과 중간재별 수량.
* BOM의 나무 구조 표현
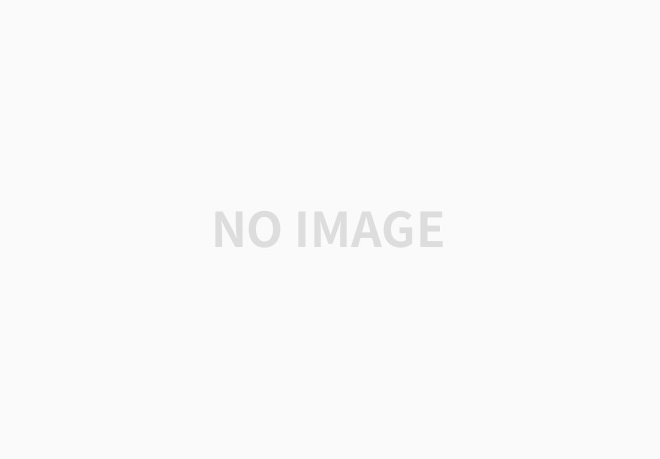
* BOM의 목록 표현
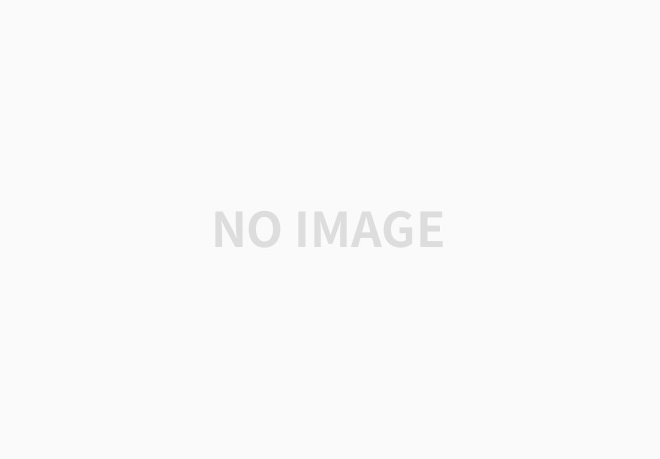
* BOM 활용 (1): 생산 단계 표현
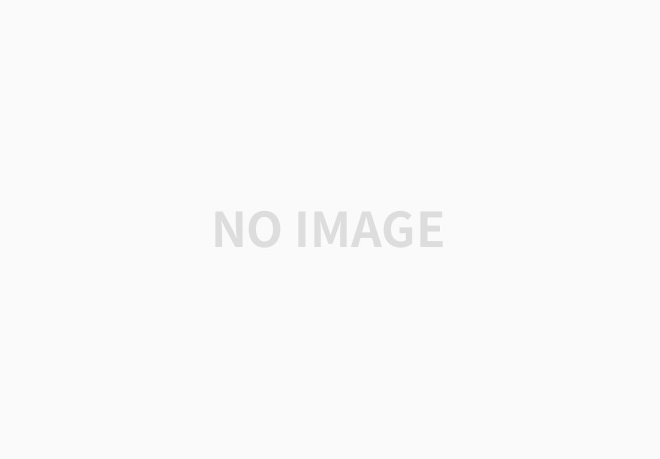
* MRP에서의 BOM 활용 (2): 필요 자재 수량 계산
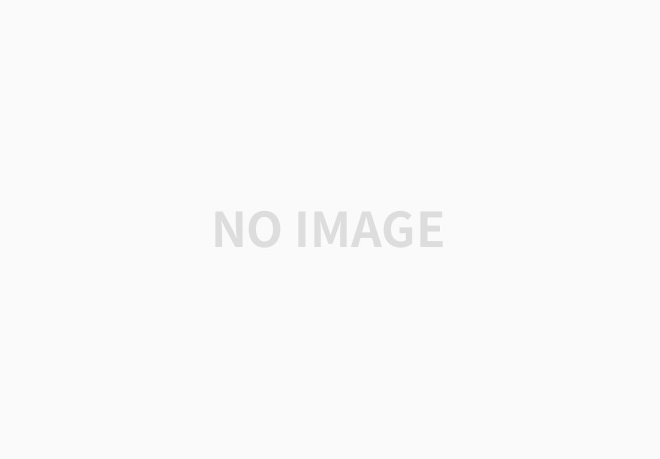
* BOM 활용 영역
제품의 구성 표현
조립과 가공 순서 표현
자재 소요량 계산
원가 산출
구매와 발주 수량 계산
부품과 반제품의 재고 관리
물류량 계획.
* 자재별 준비 리드타임
• 자재별 구매, 가공 또는 조립하는 리드타임.
구매: 발주 필요 인식부터 입고까지.
가공: 재료 이송, 설정, 가공 작업, 저장까지.
조립: 부품 이송, 설정, 조립 작업, 저장까지.
전형적인 작업 단위의 완료에 걸리는 시간.
작업 지시, 대기 등의 시간 포함.
예: 00개의 배치를 완료하는 시간
* 자재 준비의 리드타임과 제품 구조
자재들을 가공하고 조립하여 완제품을 만들어나가는 단계는 제품구조에 영향을 받는다
• 각 자재에 요구되는 준비완료 시기는 제품구조 상 상위 자재들의 리드타임을 누적하여 결정한다. (leadtime offset, time phasing)
• 완제품 생산의 총 리드타임은 제품구조에서의 리드타임의 모든 누적 경로들 중 가장 긴 값으로 정해진다.
예제의 BOM과 리드타임 기반 : 생산시점 계산
완제품부터 말단 부품까지 BOM을 따라 생산과 구매 개시 시간 역산 가능.
• 최초 부품 가공 혹은 발주에서 제품 완성까지의 최소 총 리드타임 계산 가능.
최소 8주 소요 • 각 부품 가공, 발주, 조립의 시작과 완료의 지연 한계 시점 파악 가능.
아무리 늦어도, A 납기의 6주 전에는 F, G, H로부터 E의 조립을 시작해서, 3주 전에는 완료해야 함.

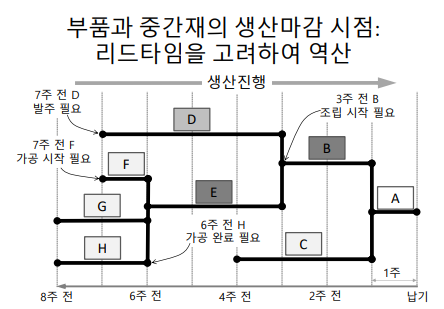
* 자재별 명목상 필요량, 실제 필요량 구별
• 재고수준 고려하여 실제 순 필요량 계산에 반영.
• 입고 예정된 양 고려.
• 안전재고 고려.
변동성 BOM, 재고 기록, 구매 수량, 생산 수량 부정확성.
* MRP에서의 소요량 계산
자재소요계획
특정 날짜까지의 특정 제품의 수요를 충족시키기 위한 자재별 계획:
• 특정 자재를 언제까지는 공급 업체에 주문해야 하는가.
• 특정 자재를 언제까지는 생산(가공, 조립)을 시작해야 하는가.
* 자재소요계획의 계산에 사용되는 요소
주일정계획: 개별 제품 모델별 생산 일정
자재명세서: 자재별 수량과 생산단계에 따른 상대적인 사전 준비 시기
자재별 리드타임: 사전 발주 시기 혹은 생산 준비 기간
재고 정보: 순 소요량 계산을 위한 재고 수준
명목 소요량 계산 예: BOM을 활용하여 전개
제품 A는 100단위 필요.
제품 A의 총 최소 리드타임은 8주
8주차 말까지 A 100단위 요구됨
A 최종 조립에 1주 소요되므로, 8주차 초에 A 100단위 조립 시작
A 조립을 위하여 8주차 초(혹은 7주차 말)까지 B 200단위와 C 100단위 필요
B 조립에 2주 소요되므로, 6주차 초에 B 200단위 조립 시작: 7주차 말에 완료 (8주차 초에 사용 준비 완료)
C 가공에 3주 소요되므로, 5주차 초에 C 100단위 가공 시작
B 조립을 위하여 6주차 초까지는 D 200*4 = 800 단위와 E 2003 = 600 단위 필요
D 발주에 4주 소요되므로, 2주차 초에 D 800단위 주문 완료
F 가공에 1주 소요되므로, 2주차 초에 F 600*2=1,200 단위 가공 시작
G 가공에 2주 소요되므로, 1주차 초에 G 600단위 가공 시작
H 가공에 2주 소요되므로, 1주차 초에 H 600단위 가공 시작
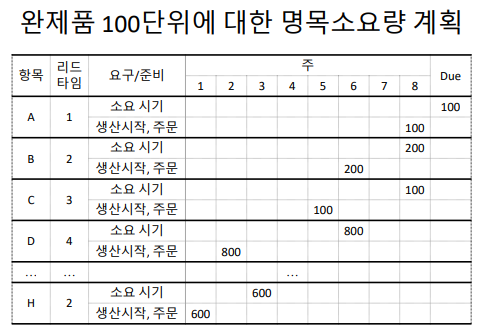
* 자재별 총 소요량 계획
자재별 총 명목 소요량 계산
- 모든 제품에 대하여 계산
- 일부 자재는 제품간 공유
- 계획 기간 전체에 대하여 시기별 계산
재고 수준 등 고려하여 총 순 소요량 계산에 활용됨.
* 자재별 명목상 필요량, 실제 필요량 구별
명목 자재 필요량 (Gross): 각 자재에 대한 생산에 투여된는 양 기준의 절대적 총 수요
순 자재 필요량 (Net): 재고수준, 재고정책 등 반영한 자재 준비 측면에서 실제로 필요한 양
- 입고예정량, 안전재고 등 고려
- 사전할당량 고려.
순 자재 소요량 계산 순 요구 량 =
총 명목 소요 예상 수량 – (현 재고 보유량 + 수령 예정 재고) + 안전재고량 + 별도 사전 할당량
* 순 요구량 계산 예
최상위 항목에서 시작: 8주차 말 A 100 단위
현 보유 재고량: A 40 단위
별도 할당량과 안전재고는 각 10, 20 단위
8주차 말 순 요구량은 100 – 40 + 10 + 20 = 90 단위
8주차 시작 시, A 조립 작업 지시량: 90 단위
A 조립에 소요되는 B의 명목 총 요구량은 8주차 시작까지 90*2 = 180 단위로 계산되고, 이 값은 B의 순 요구량 계산 절차에 명목요구량으로서 전달된다.
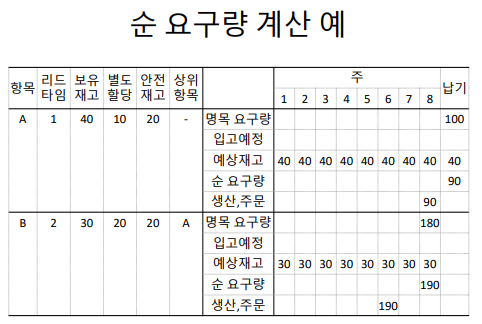
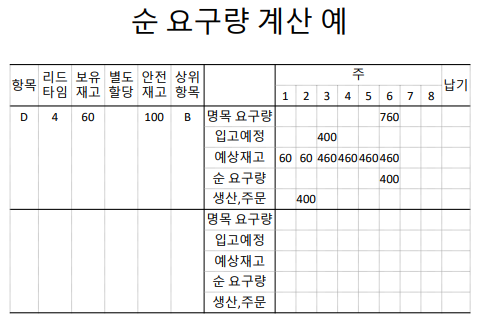
* 주문, 생산 단위 (Lot Size) 결정
• MRP에서 계산된 기간별 자재 생산량, 주문량은 실제로 집행되는 생산, 주문량과는 다름.
• 이유 :
운영의 한도: 생산 용량 한도, 최소 배치 크기, 주문 한도, 최소 주문량 등.
비용 고려: 생산 준비 비용, 주문 비용, 재고 유지 비용 등
* MRP에서의 생산, 주문 단위 결정
• MRP에서 생산, 주문 단위 선택할 수 있음.
• 기본 조건: 순소요량 충족.
• 단위 선택을 위한 규칙 혹은 알고리즘
로트 대 로트 (lot for lot) 기법: 주문량(생산량) = 순소요량
EOQ
최저비용법
MRP의 이점
• 자재의 생산, 발주와 재고 수준의 체계적 관리, 조정 가능.
고객 주문과 시장 변화에 신속하고 체계적인 대응.
• 재고 수준 감소에 활용.
불필요한 재고 축적 파악과 방지 가능.
• 설비와 인력의 체계적 관리에 활용 가능.
시기별 설비, 노동력의 요구량 파악과 활용도 개선에 이용.
* MRP의 동적 특성과 변경 제한
• 동적 시스템.
변경 사항 발생시 계획 재생성 가능.
• 계획 재생성 시, 시스템 긴장(nervousness) 현상 발생 가능.
부분적인 사소한 계획 변화가 전체적인 큰 계획 변화로 귀결될 수 있음.
• 계획 변경의 시간 범위의 제한 설정으로, 계획 재생성에 따른 시스템 불안정성 방지 가능.
* MRP의 정교함과 한계
• MRP는 수많은 요소들의 정교한 합치를 가정함.
각 요소들의 수치적 연결이 복잡하고 중층적.
작은 불합치가 계획의 큰 변화로 귀결 가능성 존재.
예: MRP의 고정 리드타임은 실제의 변동성과 불합치. 리드타임 변동, 작은 리드타임 위반이 큰 계획 오류로 확대될 수 있음. MRP는 더 하위의 세부 일정에서의 적합성을 고려하지 못함: 일정계획 상 불균형, 부하 집중, 과중 등 발생 가능.
* 유연화 (Smoothing) 적용
한 생산단위(배치, 로트) 완료 전에 작업의 일부를 다음 작업으로 보냄
리드타임 단축을 통한 시간 여유 확보
복수의 시스템에서 처리하여 작업 부하 분산
전체 작업 처리시간 단축
생산준비시간은 증가
생산단위(로트) 분할하여 분할된 일부 생산단위를 다른 곳에서 작업
* MRP의 확장
MRP의 한계를 극복하기 위한 시도들 :
JIT활용
MRP II
폐회로 MRP
용량 계획과 결합
MRP와 적시생산방법론 비교
MRP는 잘못 운영될 경우, 많은 재고와 느린 소비자 대응으로 귀결될 수 있다.
• 적시생산방식(Just in Time, JIT)는 생산시스템에서 신속하게 이동하는 작은 배치 생산에서는 더 탁월한 방법일 수 있다
• 자재소요계획 II :
MRP II 또는 자재자원계획으로 불림
생산의 다른 측면과 데이터를 활용하여 MRP 기능 확장
구매, 일정계획, 용량계획, 재고관리 기능들과 연계
환경적 측면(폐기물, 포장, 탄소배출) 등과 연계
• 폐회로(Closed‐loop) MRP 시스템은 용량 계획, MPS 등 타 생산계획에 대한 입력 제공
• 다른 생산계획 기능과의 반복순환(iteration)을 통해 MRP를 조정
• 용량계획, 유한용량일정계획과 연동
MRP에서 용량(생산자원) 요구에 대한 사항 도출.
일정계획시스템에 전달.
유한용량일정계획(Fixed Capacity Scheduling)과 병합하여 가능한 일정 생성
* 전사적자원관리계획 (Enterprise Resource Planning)
전사적자원관리 (Enterprise Resource Planning, ERP) 시스템은 MRP 시스템의 대대적인 확장.
기업 내의 그리고 기업 간의 많은 업무 절차와 과정의 자동화와 통합 추구.
구매, 재고, 물류, 생산, 판매, 인력관리 등 통합.
기업 내 공통 데이터베이스 및 방법론 공유 추구.
실시간 정보 생성 및 공유 추구.
* 일반적인 ERP 모듈의 구성
기업의 거의 모든 활동 포괄 가능.
• 기본 MRP
• 재무, 회계
• 인적 자원
• 공급망관리 (SCM)
• 고객관계관리 (CRM)
* ERP 시스템의 장점
• 공급망, 생산 및 관리의 통합 제공.
• 데이터베이스의 공통성을 창출.
• 개선된 프로세스 통합 가능.
• 사업 단위간 의사소통과 협업 증대.
• 기성품 소프트웨어 및 데이터베이스 활용 가능.
• 정보의 속도와 정확성을 향상.
• 거래 비용 절감 가능.
* ERP 시스템의 단점과 한계
• 구매, 유지 비용이 매우 높음.
• 개별 사용 기업이 자체적으로 구축하고 조정할 수 있는 수준보다 훨씬 복잡함.
• 개별 사용 기업의 전문성 부족: 업그레이드, 인력 충원 등 어려움.
• ERP 시스템의 과정과 절차가 사용 기업의 업무 절차와 맞지 않음.
* 서비스 부문의 ERP
• ERP 시스템은 서비스업 및 공공기관에도 광범위하게 활용됨.
의료, 정부, 소매점, 호텔, 교육, 금융.
아주대 학사시스템 도 ERP 시스템
• 소비자 대응 (ECR) 시스템 역할도 수행.
'생산운영관리' 카테고리의 다른 글
[생산운영관리] 공급사슬관리 (SCM) (0) | 2024.06.16 |
---|---|
[생산운영관리] 일정계획, Gantt 차트, 작업 순서 지정 (1) | 2024.06.16 |
[생산운영관리] 총괄생산계획(AP), 판매및생산계획(S&OP) (0) | 2024.06.15 |
[생산운영관리] 생산운영계획의 종류와 구조 (0) | 2024.06.15 |
[생산운영관리] 자기회귀모형, 이동평균모형, 자기회귀통합이동평균모형 (0) | 2024.05.05 |